Wire-Electric Discharge Machining
100,000+ Parts
Global Delivery
Wire-Electric Discharge Machining
Xinrong Precision is also professional in Wire-Electric Discharge Machining, and has provided high-quality services for world-renowned companies such as Foxconn, Jabil, and Han’s Laser. Based on the needs of customers with different precision and efficiency, corresponding equipment can be selected to provide services, which can save a lot of costs for customers while meeting the precision required by clients.
What is Wire-Electric Discharge Machining?
Wire cutting machining is to process parts through the discharge principle of electric spark. The workpiece is connected to the positive pole of the pulse power supply, use molybdenum wire or copper wire as the cutting wire, connect the metal wire to the negative pole of the high-frequency pulse power supply as the tool electrode, and use spark discharge to cut the machined parts. The pulse power supply provides processing energy, and the special wire cutting working fluid is used to remove the chips generated during the processing. Under the action of the electric field, the surfaces of the cathode and the anode are bombarded by the electron current and the ion current, respectively, so that an instantaneous high temperature heat source is formed in the electrode gap to melt and vaporize the local metal. The vaporized working fluid and workpiece material vapor expand rapidly in an instant. Under the combined action of this thermal expansion and the stamping of the working fluid, the melted and vaporized workpiece material is thrown out of the discharge channel, thus completing a spark discharge process. When the next pulse comes, continue to repeat the above spark discharge process to cut the workpiece into shape. The wire cutting trajectory is controlled through CNC programming to complete the final workpiece shape.
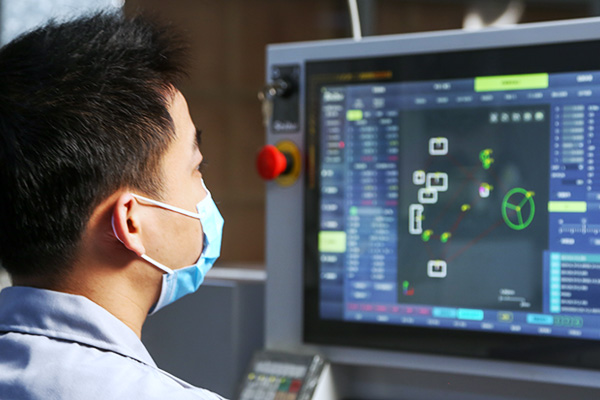
Why choose wire-electric discharge machining?
The quality of the machined surface is close to the grinding level, the wire cutting process is stable, uniform, with little jitter, good processing quality, and high production efficiency, which can reach 350/min. The wire cutting machine adopts the method of continuous wire feeding of electrodes, and the electrodes can be supplemented when they are lost, so the machining accuracy can be improved. The surface roughness value of the workpiece processed by the slow-moving wire cutting machine can generally reach Ra0.8μm and above. It can meet most of the workpieces with high hardness and ultra-high precision requirements.
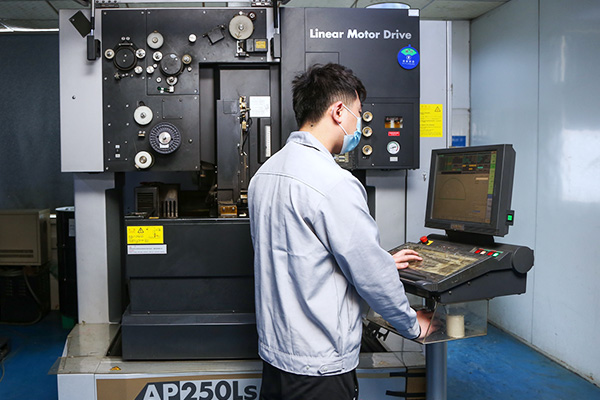
What materials can be used for wire cutting?
Conductive metal and graphite can be used for EDM, common tungsten, brass, bronze, carbon, graphite copper, carbon steel, stainless steel, inconel alloy and so on.
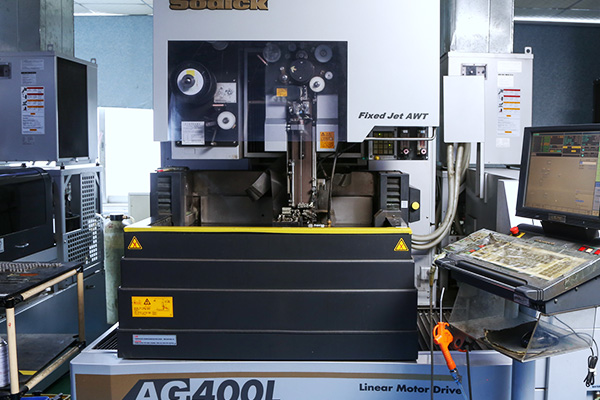
Advantages of Xinrong Precision for Wire-Electric Discharge Machining:
1. Our equipment is highly precise, and our team is professional and skilled in dealing with hard products; all problems can be solved when conceding complex products.
2. We have introduced almost 20 sets of cutting machines in the brands of Sodick and Seibu from Japan, ensuring mass production in high precision.
3. Our rich experience can optimize the manufacturing proposal for clients with only design drawings, saving cost.
Wire-Electric Discharge Machining
Contact us for a free quote
Our engineering team promises to offer you a quote within 24 hours after receiving your design files, and the waiting time can be cut if the file involves less degree of complexity. Our sales will keep in touch with you to ensure the quote to be handed to you.
FAQ:
1. What is the precision of Wire-Electric Discharge Machining in Xinrong Precision?
Our equipment that is introduced from Japan can ensure high precision of 0.005mm.
2. What is the maximum size and weight of your product?
Our maximum size or products is 560mm*350mm*300mm, and the maximum weight is 100Kg.
3. Can you process special alloy material?
Conductive materials can be processed by wire cutting.
4. How many products can your cutting machines make per month.
The production scale varies with the degree of complexity; 10,000 to 100,000 parts can be manufactured monthly.
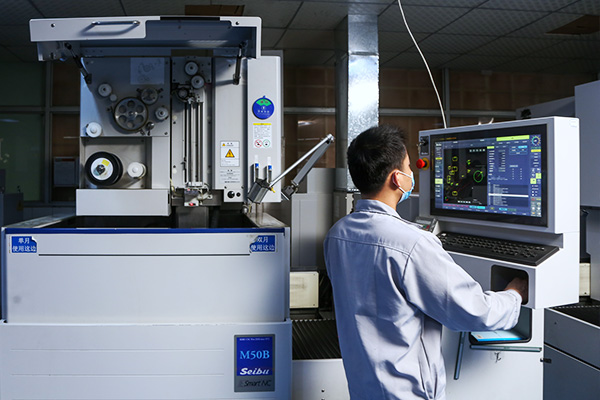