Post-Processing
100,000+ Parts
Global Delivery
Post-Processing
At Xinrong Precision, we are not only capable of providing one-stop machining, but also post-processing services required by clients.
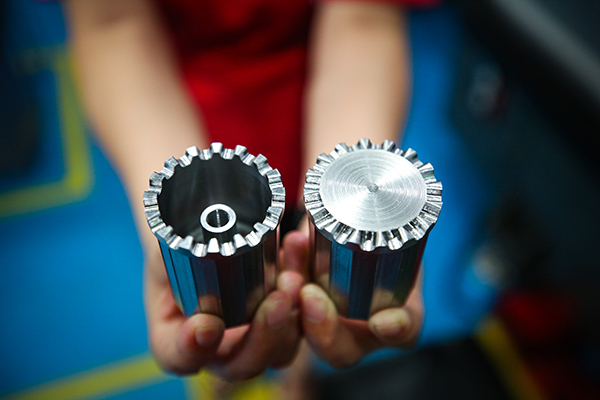
A full range of professional post-processing services:
We are not only able to produce jigh-quality parts but also provide corresponding post-processing services for your parts to improve their appearance, performance and wear resistance. The post-treatment services we provide contain: electroless nickel plating, nickel electroplating, zinc plating, anodizing,sand blasting, polishing, passivation, heat treatment.
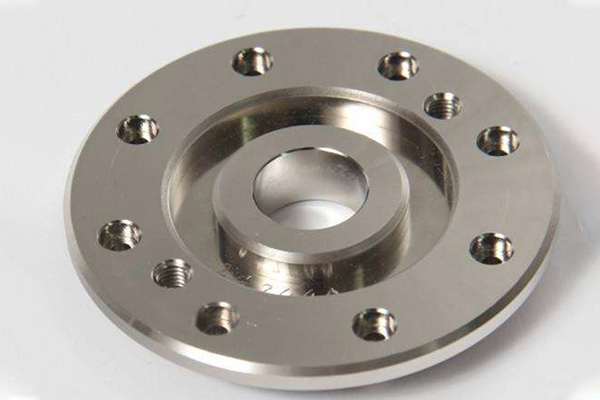
Electroless Nickel
Electroless nickel plating is a process of reaction in a nickel-phosphorus alloy deposits on a metal surface, which uses a pure chemical reaction to induce nickel plated without electricity. Although this process is much longer than electroplating, the advantages are a more uniform thickness (since there is no need to rely on a changing electric field), and better wear and corrosion resistance even on the most complex surfaces sex.
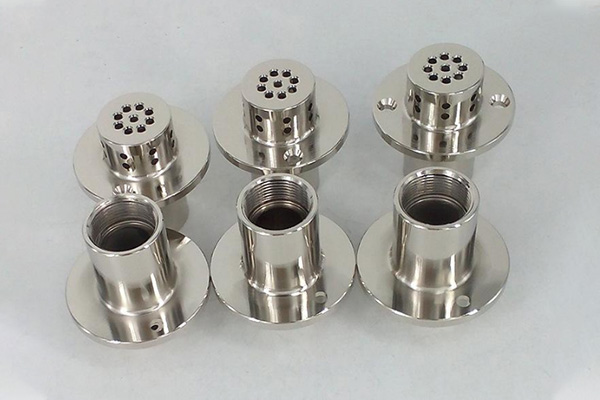
Electro Nickelling
Nickel plating is the process of electroplating a thin layer of nickel on metal parts. This coating can be used for corrosion and wear resistance and also for decorative purposes. When the parts are cleaned, they are immediately submerged in the electrolyte. The nickel anode is then dissolved into the solution and deposited on the part that acts as the cathode in the reaction.
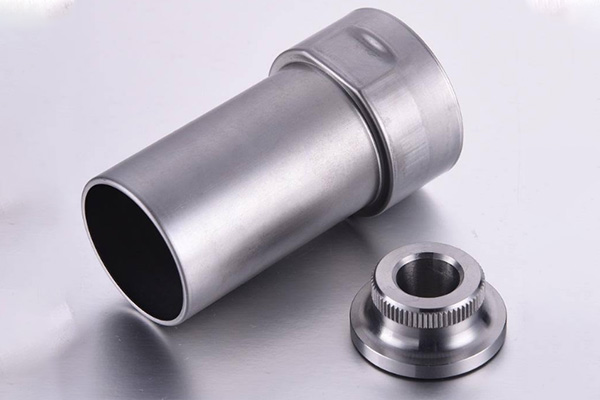
Zinc Plating
This technology is used to prevent surface oxidation or corrosion. This process is done by applying a layer of flux to the workpiece and then dipping the workpiece in molten zinc. The molten zinc combines with the steel to form a protective layer on the surface of the part.
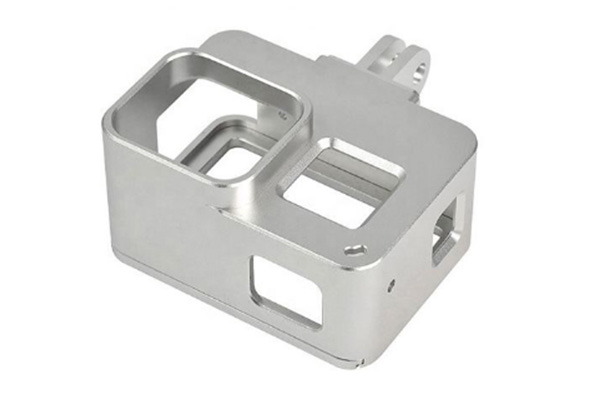
Anodic Oxidation
Anodizing is an electrolytic passivation process that creates a natural oxide layer on aluminum parts to prevent wear and corrosion, and to make the part aesthetically pleasing. It is a conversion coating, which means that the surface of the aluminum shrinks in size before the protective oxide layer builds up. When this process is complete, the oxide layer is underneath the intact aluminum sheet, which means it won’t peel or peel.
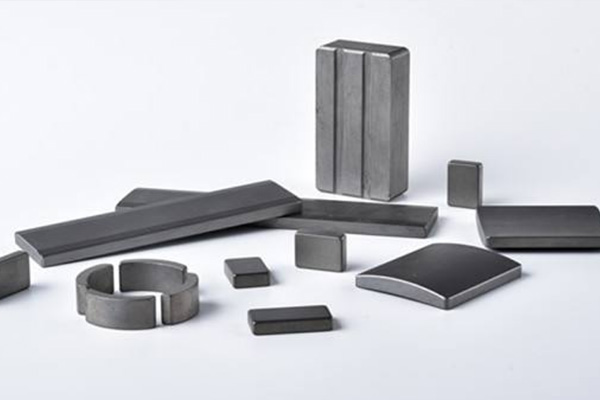
Passivation
The mechanism of passivation can be explained by thin film theory, that is, passivation is considered to be due to the action of metal and oxidizing substances, and a very thin, dense, well-covered, and firmly adsorbed metal surface is formed on the metal surface during the action. passivation film. This film exists as a separate phase, usually a compound of metal oxides. It has the function of completely separating the metal from the corrosive medium, preventing the metal from contacting the corrosive medium, so that the metal basically stops dissolving and forms a passive state to achieve the effect of anti-corrosion.
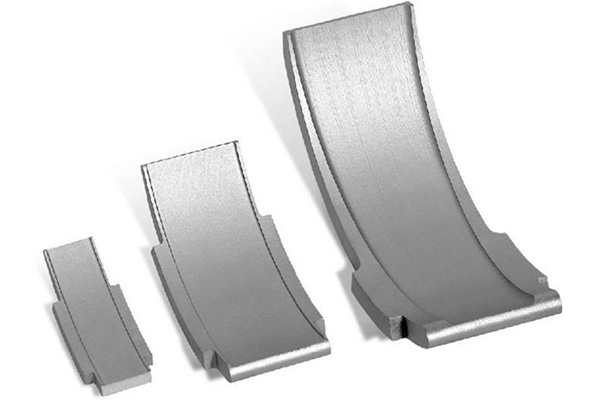
Sand Blasting

Polishing
Polishing refers to the use of mechanical, chemical or electrochemical action to reduce the surface roughness of the workpiece to obtain a bright and smooth surface. It is the modification of the surface of the workpiece by using polishing tools and abrasive particles or other polishing media.